Vervaardigen van de kast
Lamineren van houtfineer om de rim te vormen
Laten we ons eerst eens richten op het maken van de rim.
De onderstaande foto's tonen houtfineerlagen die in de lengte zijn samen gelijmd om een laag van de rim van de vleugel te vormen. Deze lagen worden samengevoegd tot één lang geheel door ze te verlijmen en te lamineren. Het aantal lamineringen van deze lagen varieert afhankelijk van het model, maar ligt meestal tussen de 6 en 10.
Zodra het lange gelamineerde houten geheel is voltooid, wordt het in een pers geplaatst die hoogfrequente energie gebruikt om het hout te verwarmen, en hydraulische druk om het geheel in een grote vorm te persen, die de typische vorm van een vleugelkast heeft. Vervolgens wordt er met hars geïmpregneerd papier aan de buitenkant van de rim gelijmd voor een ontvankelijk oppervlak voor het latere afwerkingsproces.
De binnenste rim, die een frame vormt aan de binnenkant van de rim, wordt op een soortgelijke manier gemaakt.
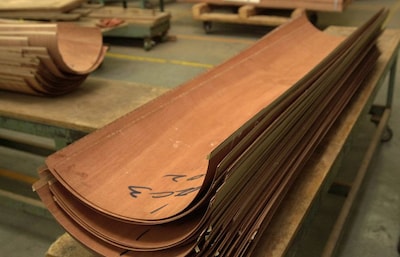
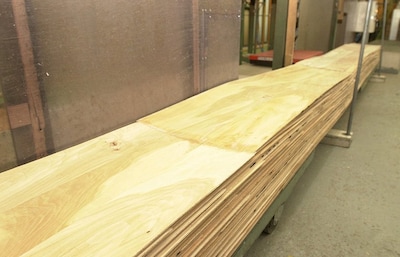
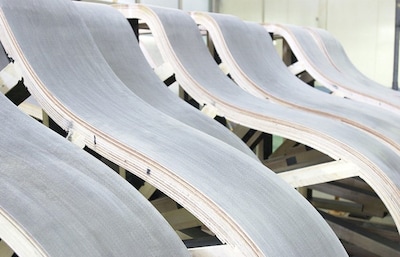
De binnenste rim en buitenste rim combineren
Vervolgens wordt de binnenste rim, die de gebogen contour van de buitenste rim ondersteunt, met rechte balken samengevoegd tot het structurele frame van de piano. De balken worden met traditionele zwaluwstaartverbindingen in de binnenste rim bevestigd en het oppervlak wordt plat geschaafd.
De zangbodem komt later op de binnenste rim te rusten, die zo gefreesd wordt dat hij precies past. De bovenkant van de zangbodem heeft een kroon (een lichte bolling) die bolt richting de snaren, en de bovenlaag van de binnenste rim wordt onder dezelfde hellingshoek ingesneden. Daarnaast worden een aantal verstevigingsribben aan de onderzijde van de zangbodem gelijmd en worden er sleuven in de binnenrand gefreesd waar deze ribben in passen. Tot slot wordt de buitenste rim, die op een bepaalde temperatuur en vochtigheidsgraad is afgestemd, met de binnenste rim verbonden tot één eenheid door middel van verwarming via hoogfrequente inductie.
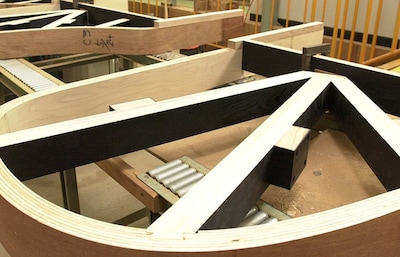
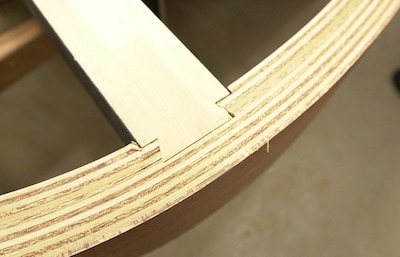
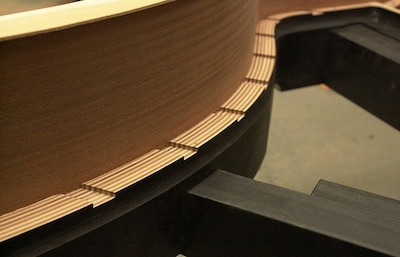
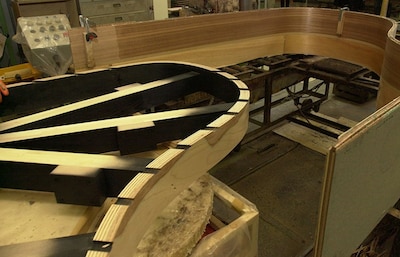
Afwerking
Voor het afwerkingsproces wordt een robotsysteem gebruikt. Eerst wordt een grondlaag opgespoten en warm gehouden zodat het snel droogt en uithardt. De uiteindelijke toplaag wordt in de vorm van een extreem fijne nevel aangebracht, gevolgd door een polijstproces dat resulteert in een aantrekkelijk, prachtig afgewerkt oppervlak.
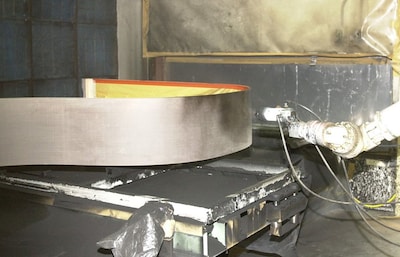
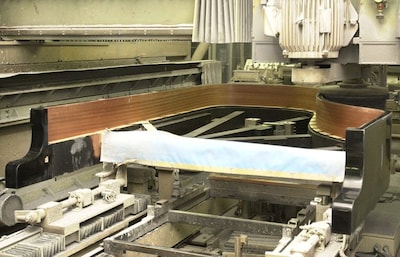
Het maken van de zangbodem, het deel dat de klank bepaalt
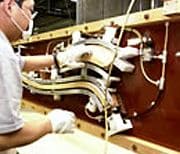
De zangbodem vormt het hart van de piano en hoe het tot stand komt is een belangrijk proces voor wat betreft de klank.
De zangbodem is een dun houten blad, gemaakt van zorgvuldig geselecteerde Sitka-sparren of Japanse sparren. Vóór gebruik wordt het hout aan de lucht of via ovens gedroogd tot een bepaald vochtgehalte. De zangbodem is opgebouwd uit vele kleine plankjes die aan elkaar gelijmd zijn van rand tot rand. Het grote blad wordt in de gewenste vorm gesneden en tot de juiste dikte geschaafd. Vervolgens wordt het speciaal geconditioneerd (gedroogd) voor de klimaatomstandigheden van het land waarin de koper van de piano woont.
Daarna worden er ribben aan de onderzijde van de zangbodem gelijmd in een richting die loodrecht op de nerf van de afzonderlijke planken in de zangbodem staat. Dit gebeurt zodanig dat de geluidstrillingen gelijkmatig door de hele zangbodem worden doorgegeven en dient ter versterking en versteviging van de zangbodem die horizontaal gezien zwak is. De lange kam en de korte kam worden aan tegenovergestelde kanten van de ribben bevestigd.
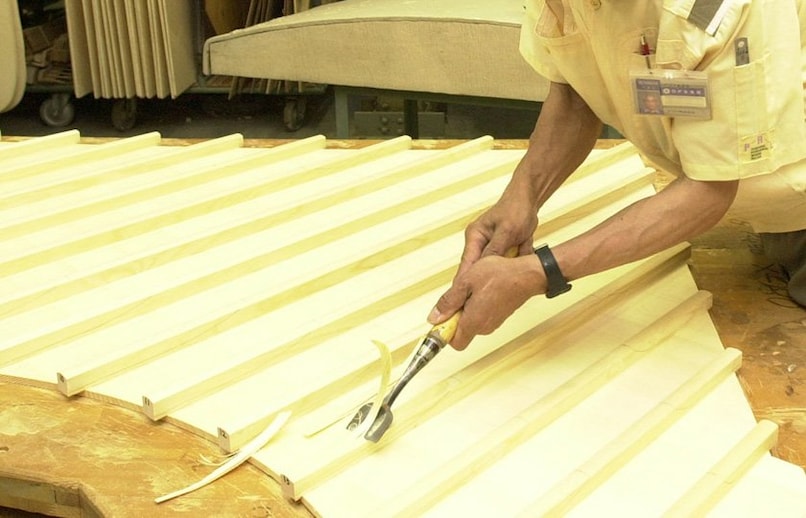
Bevestig het frame en de kast is bijna compleet!
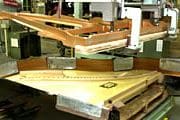
Zodra de afgewerkte zangbodem op zijn plaats is gezet op de binnenste rim en het metalen frame erop is bevestigd, is de piano bijna voltooid.
Het frame is in principe gietijzer gemengd met enkele extra metalen voor akoestische kenmerken. De metalen worden gesmolten, gemengd en in een mal van zand gegoten om af te koelen en uit te harden. Het frame weegt ongeveer zo'n 100 tot 150 kg.
Muziekinstrumentgids: Piano-inhoud
Oorsprong
Opbouw
Hoe te spelen
Vervaardiging van het instrument
Een instrument kiezen
Onderhoud en verzorging
Trivia
- De kleuren van de witte en zwarte toetsen op piano's waren andersom in Mozarts dagen
- Had de piano van Mozart een pedaalklavier?
- Piano met automatisch begeleidingssysteem in de dagen van Beethoven
- De piano's geliefd door de grote meester: Svjatoslav Richter
- Het optimale materiaal voor pianoframes is ook ideaal voor motoren van motorfietsen
- De zangbodem van een piano is een plaat die ook trillingen stopt
- Waarom kan een piano niet meer dan 88 toetsen bevatten?
- Waarom een voelt het bespelen van een toetsenbord van een vleugel zwaarder aan dan dat van een staande piano?